Preventive Hose Maintenance: 7 Essential Steps for a Comprehensive Plan
Knowing when to replace industrial hoses is a major concern for plant managers and engineers alike. Delaying the replacement of hoses in need of attention can significantly increase the risk of failure, which can lead to safety hazards and unplanned downtime. Conversely, replacing hoses too early, while not a safety risk, can be expensive in terms of time and money.
Why preventive hose maintenance?
To address these concerns, a preventive hose maintenance plan can complement standard operating procedures by providing information on every hose in your Australian plant. This involves monitoring the lifespan and performance of each hose, conducting frequent inspections, proactively replacing them, and identifying key replacements to have on hand. While creating such a plan may seem daunting, the cost-saving benefits make it well worth the initial investment of time. Each hose in your facility experiences different application parameters and thus requires a unique replacement interval based on its environment. Factors such as pressure, movement demands, and nearby equipment should all be taken into account.
For example, consider a process application that uses 50 identical hoses in an hose plant. Half of these hoses are steam-cleaned and have a lifespan of one year, while the other half are not cleaned but can last up to five times as long. Using a five-year maintenance cycle for all hoses can be risky and may result in costly shutdowns due to unexpected hose failures. On the other hand, using a one-year replacement interval for all hoses would mean prematurely replacing hoses that still have years of useful life remaining. If the plant were to increase the replacement interval for the second set of hoses to five years, at a cost of approximately US $250 per hose, the savings in product costs alone would amount to AU$25,000, not to mention the value of reduced maintenance and downtime.
Creating a preventative industrial hose maintenance plan: 7 essential steps
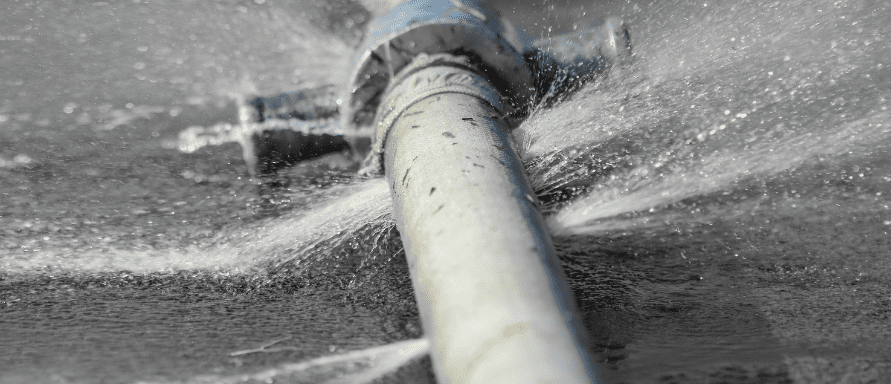
Your hose supplier can offer you general guidelines for inspecting and replacing your hoses, but the actual intervals will vary depending on the operating environment, construction materials, and other factors. These intervals are unpredictable and can only be determined through careful observation and record-keeping.
Follow these steps to develop a successful preventive maintenance plan for your industrial hoses:
1 . Identify and tag all your hoses
Conduct a comprehensive audit of your plant, including identifying and tagging every hose. Take detailed notes, including the type of hose, part number, process fluid, pressure or temperature ratings, and the vendor’s contact information. Create a spreadsheet to record additional details, such as the hose’s length, size, core material, construction, reinforcement layers, end connections, mounting, cover type, operating conditions, cleaning procedures, and installation and replacement dates. This process alone can be a valuable addition to your plant’s operating system. If you are unsure where to begin, consult with Certags experienced team, who can evaluate your systems and provide you with tailored advice and support.
2. Monitor the lifecycle of each hose
Schedule regular hose inspections, based on the supplier’s recommendations. These inspections are mainly visual and do not usually require system downtime. Look for signs of wear, such as scrapes, cuts, corrosion, kinks, and general deterioration. Record all observations in your spreadsheet.Once a hose has reached the end of its life, make a note of its service interval. This information provides a known replacement period for that hose. In case of a hose failure during operation, document all details, including the location of the failure, the severity of the break, and how the hose was mounted. These details will help you troubleshoot the failure with your hose supplier and prevent a recurrence.
3. Reduce hose strain
During inspections, identify any conditions that put undue strain on your hoses, such as rubbing against equipment, exposure to external heat sources, pulses, or unfavourable arrangements. Correct these situations immediately as they may shorten the service life of your hoses or cause failure.
4. Protecting hoses with covers
Depending on the operating environment, some hoses may require protective covers such as Thermo sleeve, fire jacket, spiral guard, armour guard, or spring guard, to protect them from abrasion, kinking, or extreme temperatures. Careful consideration must be given to each option’s operating temperature and functionality to choose the best protective cover for each hose.
5. Regular inspection and replacement protocols
After determining the replacement interval for each hose, periodic inspections should continue to ensure that any changes in system parameters do not place a strain on the hoses. Regular visual inspections are a crucial part of preventative maintenance, and they are also one of the simplest steps to perform. Depending on your application, the hose system and fittings should be inspected daily, weekly, or monthly. A list of signals that indicate a complete shutdown and replacement of the hose assembly to quickly address any problems that arise could come in handy.
These signals should include leaks in or around fittings, displaced or slipping fittings, visible damage to fittings such as cracks and corrosion, signs of damage to hoses such as cracks, charred surfaces, unusual stiffness, kinks, twists, flattened or crushed portions, and damaged covers such as cuts, abrasions, blisters, and cracks, particularly if the damage exposes the reinforcement, which requires replacement as soon as possible. Finally, loose, soft, or degraded covers should also be inspected and addressed as needed.
6. Analysing data
Periodically analyse historical data against established hose inspection and replacement frequencies to determine if any intervals should be shortened or lengthened. Destructive testing of replaced hoses can indicate if a hose was replaced too soon or too late. If a particular hose is frequently replaced, consider an alternative design that offers a longer life.
7. Spare hose inventory
Order replacements in advance, and keep spares of critical safety or process hoses, those likely to fail, and those for special applications. This inventory will help prevent costly downtime and delays.
Meticulous record-keeping and regular inspections may require an investment of time, but the cost savings and safety improvements are well worth it. A well-planned hose maintenance program can increase profitability, enhance safety, and reduce downtime.