How to get started with 5S Red Tags to better organise your workplace
Learn about the 5s lean manufacturing methodology and 5s tagging system
Keeping the workplace organised and clean can seem an overwhelming task, above all when hundreds of tools and equipment are used. However, with the right guidelines and by implementing processes, it is just a matter of time to have a more efficient workplace and to reduce wastage.
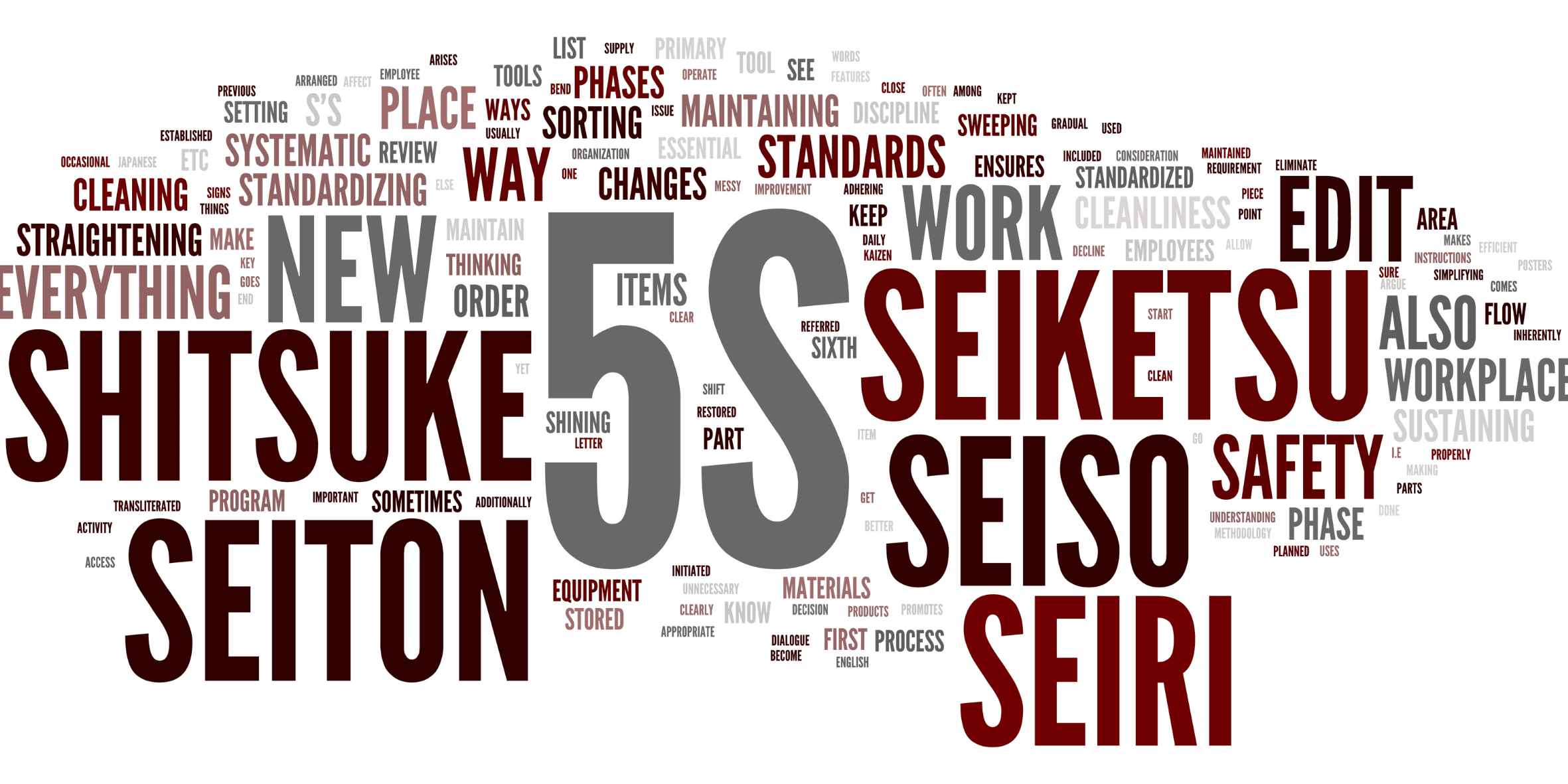
What is 5S?
The 5s lean system is a methodology started in Japan, that was first implemented by Toyota’s production system to better organise and maintain the workplace, in order to improve efficiency. This methodology is derived from the Japanese concept of kaizen, which is focused on continuous improvement.
The goal of 5s Lean Manufacturing is to create a workspace that is safe, efficient, and easy to work in. The methodology is based on avoiding or reducing at minimum any sort of waste, from unused tools to time wasted looking for them.
5S refers to five Japanese terms used to describe the steps of the 5S system of visual management which are:
- Seiri = Sort: sort and remove all the unnecessary items in your workplace (machinery, tools, paperwork..)
- Seiton = Set in order: rearranging the useful items in order to make them easy to find
- Seiso = Shine: take care and maintain tools and equipment in order to have an organised workplace and extend their lifecycle
- Seiketsu = Standardise: standardised the best workplace practised it helps to ensure high quality, deliverability and safety
- Shitsuke = Sustain: this step is all about building a culture of order and discipline in the workplace and making sure it is implemented long-term
What items can be used for implementing a 5s methodology?
- Labelling system: implementing an effective labelling system can help improve the workplace’s organisation and structure. Despite the industry, pretty much every tool, equipment or item can be labelled for better visualisation and recognition. An example? Shelves, racks, toolboxes, offices and workspaces, specialty equipment and so on. Labelling makes it easier to find tools and it also it makes easier to identify if something is missing or out of place.
- Signs: signage in a workplace is fundamental to increasing overall safety. They highlight the presence of hazards, and dangerous areas by using direct visual communication.
- 5s Red Tags: they are part of the first step of the 5s methodology and they can help get rid of unused tools, machinery or items that are no longer profitable in a workplace. The 5s red tags are attached to assets that are no longer providing value to the business so employees can decide is time to get rid of them.
- Label printers: having in-house printing can be a convenient and cost-effective method to implement a 5s methodology strategy, as labels can be just printed when needed without relying on an external source.
- Floor markings: same as signs, floor markings can be applied in dedicated areas to warn of dangers, and hazards or simply to delimit certain areas for organisational purposes.
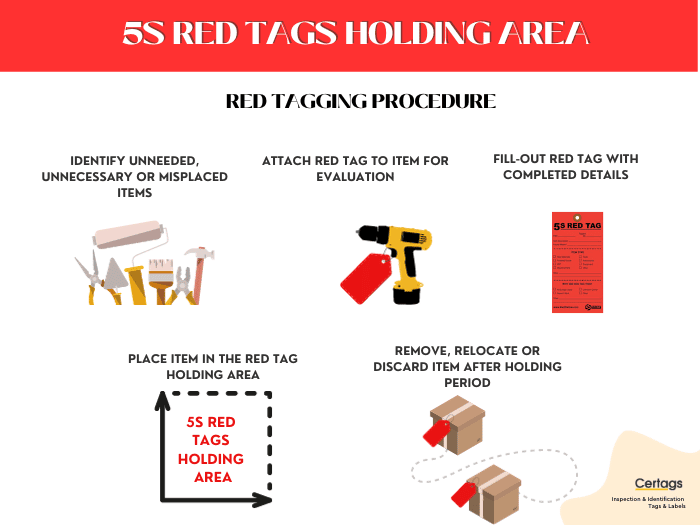
How to get started with the 5S red Tags strategy?
The first step of the 5S lean methodology is “Sort” and it has the goal to remove all unnecessary objects and create a clean work environment; in addition to that, it also helps employees to change their behaviour and take responsibility of all assets that are present in the
workplace.
Implementing a 5s red tag strategy is the first action to take for a better and organised workplace, to start getting rid of clutter that can prevent employees to work efficiently and also to educate them in keeping a clean workspace.
With the help of 5S red tags, employees can realise how much of what they have around them is unused and is taking up space and can help them organise items that can be thrown away, recycled or even reused or repurposed. This cost-effective process will lead to improved efficiency and productivity that will benefit the overall organisation.
Steps to Implement 5s Red tags strategy:
- Identify an area of the warehouse or factory to focus on as a start;
- Choose criteria for selecting the tools: for example, choosing the tools that are essential for that specifically designated area or job function;
- Ask the team to browse through all the tools, items and equipment that are present in that specific area and ask them to apply a Red Tag on all the items that don’t align with the chosen criteria;
- A red tag should include the location, who found the item, and the date it was found; There are two sides to the tag to allow enough space to write key descriptive statements
- Organise a designated red tag holding area where you can transfer all the items that have been red-tagged;
Keep the tagged items in the designated area for a limited amount of time (typically 1-2 months). Any item that has not been used while being the holding area for a month should be thrown away or recycled. The other items should be stored (for seasonal products) or moved to an area that uses the item.
When is the right time to action a 5s red tag strategy?
- When you need more visual control over all items and assets in your workplace;
- When there are multiple departments working in the same work environment;
- When you or your employees waste a lot of time looking for things;
- The working area is large and the sorting process will take quite a bit of time;
- There are many unused and unnecessary items;
- You want to use certain areas of the factory or warehouse more efficiently.
Certags has specially designed 5S Red Tags for use in any organisation and industry. Contact us to get started!